Patterns and Performance
Toni Stabile Student Center
Introduction
This project, a new Student Center for Columbia University’s Graduate School of Journalism, transforms both formal and informal work, meeting, and social spaces of the school. The student center becomes a nexus for the flow of the academic life of the building through the renovation of a large multilevel interior and slipping a new addition onto the campus that links the journalism school to the broader campus community. Digital design and production technologies facilitate an investigation of the performance of the primary materials. Four separate episodes within the architecture of the project engage in the technical (quantitative) while also critically engaging in the cultural or phenomenal (qualitative) implications of digital design and production. The four zones of architectural research involve highly engineered surfaces, each of which is generated through digital processes to address a particular technical or programmatic requirement, while also designed to produce specifically architectural or experiential effects. These surfaces thus satisfy a double definition of the word performance: by performing on two levels, the technical/quantitative and the phenomenal/qualitative, the project offers a new model for implementing digitally-driven design.
A team of specialists was put together to contribute to the development of the specific performance criteria and digital modeling for each surface of this project. The approach was to expand our network of allied consultants to ensure that the technical performance is optimized while managing the flow of information and communication to guarantee that the qualitative implications of the design remain linked to the overall goals of the project. Digital modeling is utilized to engineer performance but also to test and innovate architectural effects. Working closely with fabricators, each surface system was put through rigorous prototyping. While technical performance can be numerically driven and calculated, the cultural and qualitative effects of each surface were tested at full scale to achieve the desired resolution and legibility. The techniques of the assembly for each patterned surface were finalized in the prototyping phase, with information and coordination of the assembly logics embedded in the final digital files.
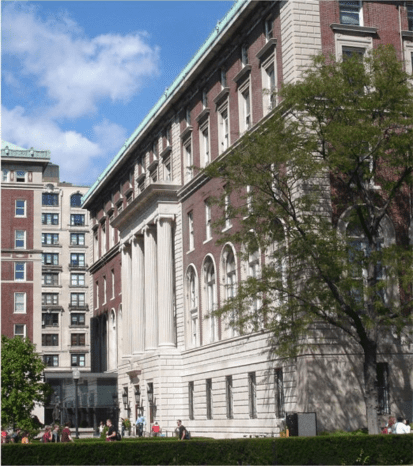
Context:
Columbia University Graduate School of Journalism
The project consists of two phases: (1) a 9,000 s.f. complete renovation of two floors of an existing McKim, Mead & White building on Columbia University’s Morningside Heights campus, and (2) a 1000 s.f. glass addition. The renovation provides a new student “social hub”, flanked by the Journalism Library, faculty offices, classrooms, and a student newsroom. The new addition is located in a previously unused exterior plaza, sandwiched in between the Journalism building and an adjacent dormitory, and will provide a new student lounge and cafe space open to the University community.

The first phase was completed in December 2007, and the second phase is currently under construction with completion scheduled for August 2008.
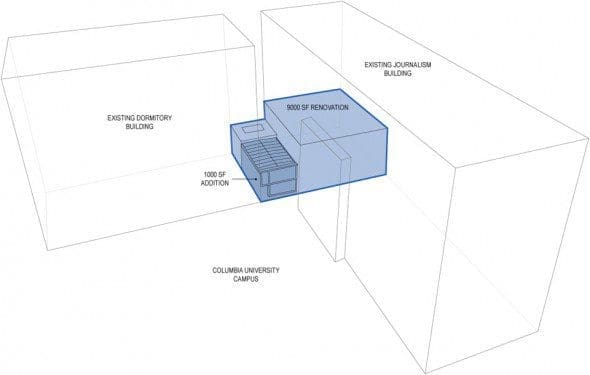
Patterns & Performance
Four surfaces are used to test different strategies of double performance-driven design. These surfaces consist of the ceilings and walls in two of the project’s primary spaces: the interior “Social Hub,” essentially a study area and meeting space for students and faculty; and the new cafe addition, which is a more public venue for the School and the University. The strategies adopted for designing and engineering each surface arise directly from technical and programmatic demands for each space.

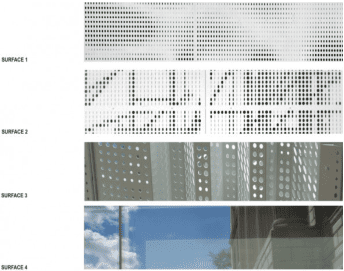
Surface 1: Acoustic Performance
Performance Criteria: Eliminating acoustic reverb and echo in a multi-function space.
The ceiling of the Social Hub, comprised of perforated 16-gauge steel panels backed with acoustic insulation, is designed to provide an acoustically absorptive ceiling for a room that accommodates a wide range of uses (study area, meeting room, lecture hall, event space). The geometry of the ceiling wraps tightly to existing building structure to increase ceiling height where possible. The logic of the perforation pattern was developed through a two-phase process: first, an acoustic model of the space was developed to drive the density of perforations, and a second subsequent scripting process integrated geometry, lighting, and sprinkler layout into the pattern generation.
Pattern Generation: Acoustic Modeling
An acoustic model of the space was developed to establish the performance criteria for the ceiling’s perforation pattern. Several scenarios were generated within the software to identify the zones of the ceiling that, through increased acoustic transparency, would reduce and eliminate reverb and echo effects in the space. These points then became “zones of intensity” or “attractors” for the pattern generation script—areas where the perforations would become larger and provide more acoustic absorption.
The pattern script was developed to generate a series of unique iterations, each of which relied on the attractor points and thus satisfied the acoustic performance criteria for the space. The iterations were evaluated both for the density of perforations (which translates directly to fabrication time and cost) as well as overall qualitative effect.
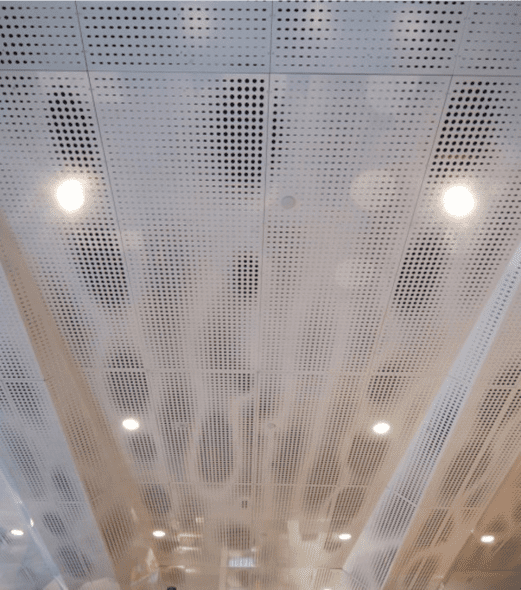


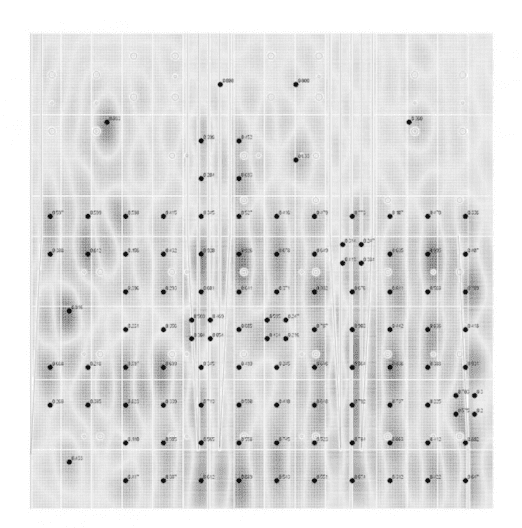
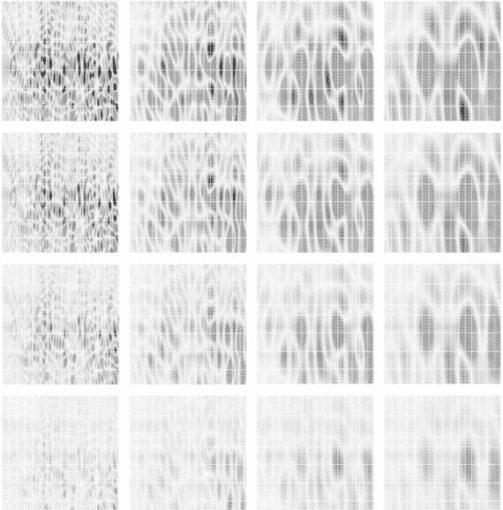
Pattern Generation: Scripting
The second phase of designing the perforation pattern involved calibrating the scripting process to respond to the preexisting conditions in the ceiling, as well as various forms of infrastructure that would be integrated into the ceiling. Rules were developed to establish “buffer zones” adjacent to light fixtures, sprinkler heads, edges of panels, and the break/bend lines of the panels. Through a digital scripting process, the pattern generated from the acoustic analysis was modified accordingly to accommodate these rules.
RULES:
(1) All holes on 1 1/2” grid.
(2) All holes can infinitely vary from I’ diameter circles to 5/8” long ovals.
(3) No holes within 1” of panel joint lines.
(4) Any hole within 6” of panel joint lines must be less than 1/2” in diameter.
(5) No holes within 1/2” of light/sprinkler cutouts.
(6) Any hole within 6” of light/sprinkler cutouts must be less than 1/2” in diameter.
(7) No holes within 1” of bend lines.
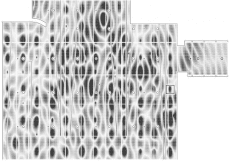

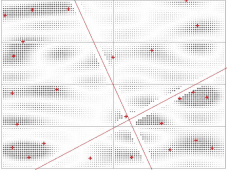
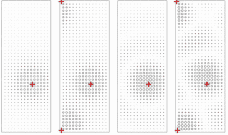
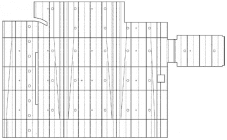
Fabrication & Assembly
The digital modeling of the ceiling and the perforation pattern enabled an easy translation directly to the fabrication and assembly process. The shop drawing phase was eliminated; digital files for each ceiling panel were taken directly from the model and used by the fabricator for both laser-cutting and bending the panels.
The ceiling panels are fastened to a grid of steel tubes with holes pre-cut to match precisely with corresponding holes in the panels. The entire system is hung from a standard ceiling suspension system.
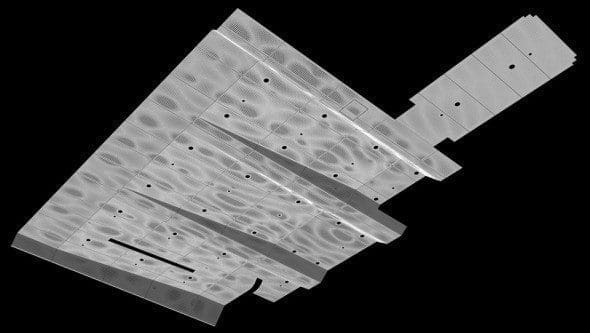
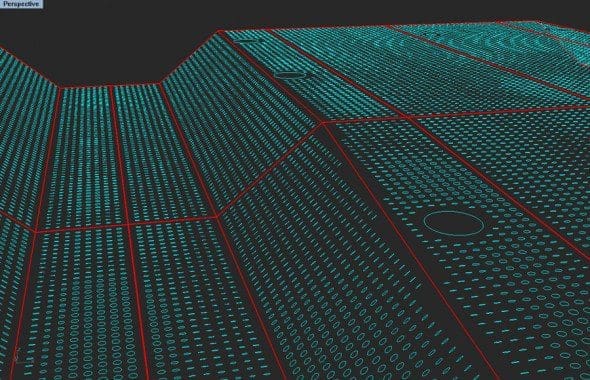
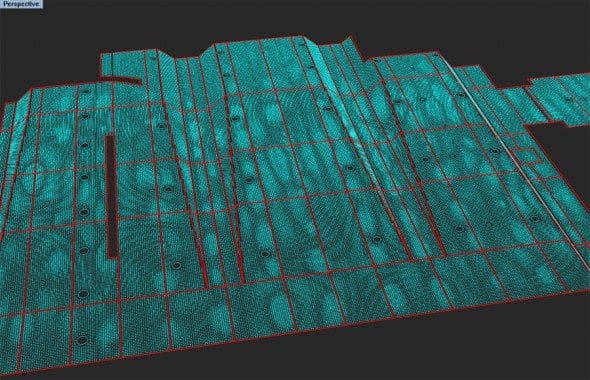
Surface 2: Cultural Performance
Material: 13 ga. perforated steel (powder-coated)
Performance Criteria: Projecting an image that provides multiple readings at different scales and proximities.
The west wall of the social hub was designated by the client to be a primary design feature for the new student space. Extending from the social hub down through a new opening in the floor slab, the wall connects the upper space with the new student newsroom below. The specific performance criteria for the wall were developed through research into how pixelation and resolution could be utilized to provide variable effects and perceptions from different locations in the room. Generating the pattern thus became a question of balancing digital tools of image conversion with full-scale tests of the resultant qualitative effects.
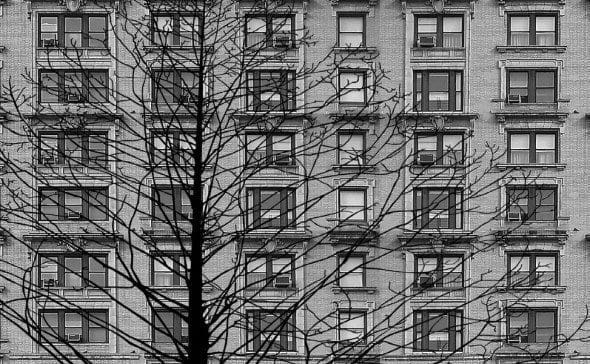


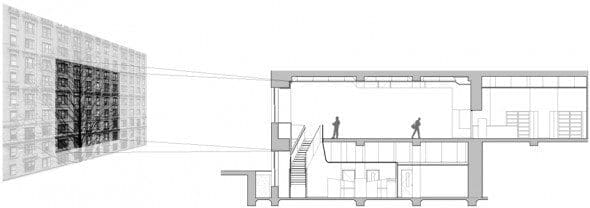
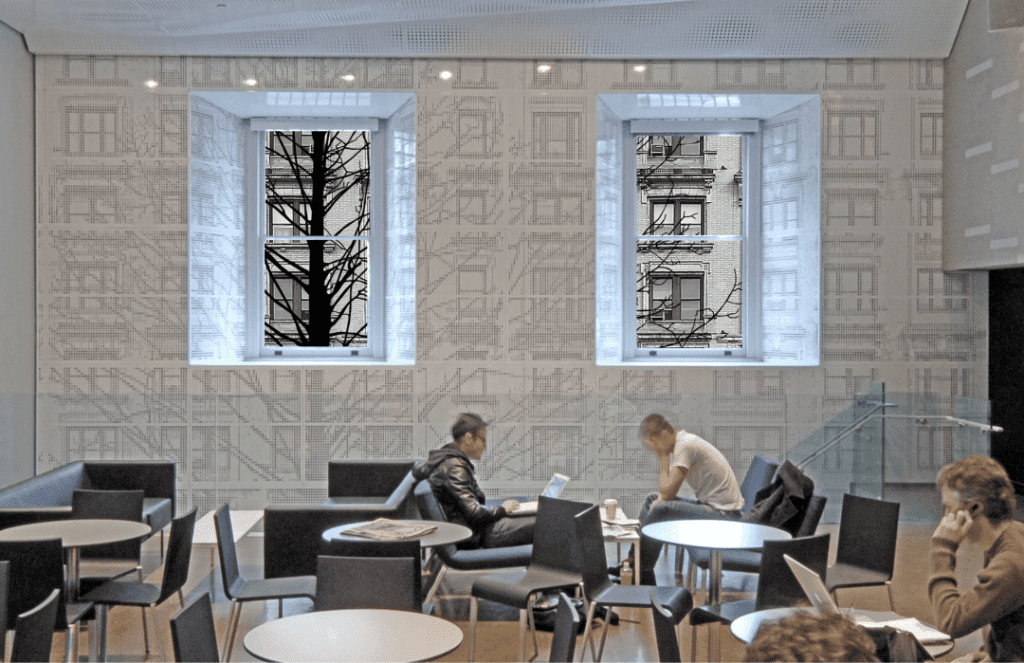
Pattern Generation: Rules
The pixelation scripting process uses an alphabet of six discrete “characters,” each corresponding to a specific range of tonal values within the black-to-white spectrum. Through a simple algorithm, the script converts the image into a perforation pattern by replacing the raster information with characters according to tonal value. The characters consist of a gradient from zero (“O”) to one (“1″) — literally, the most basic forms o
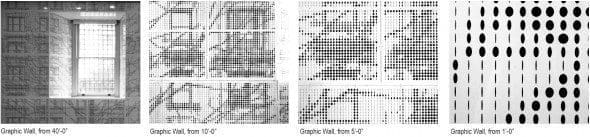
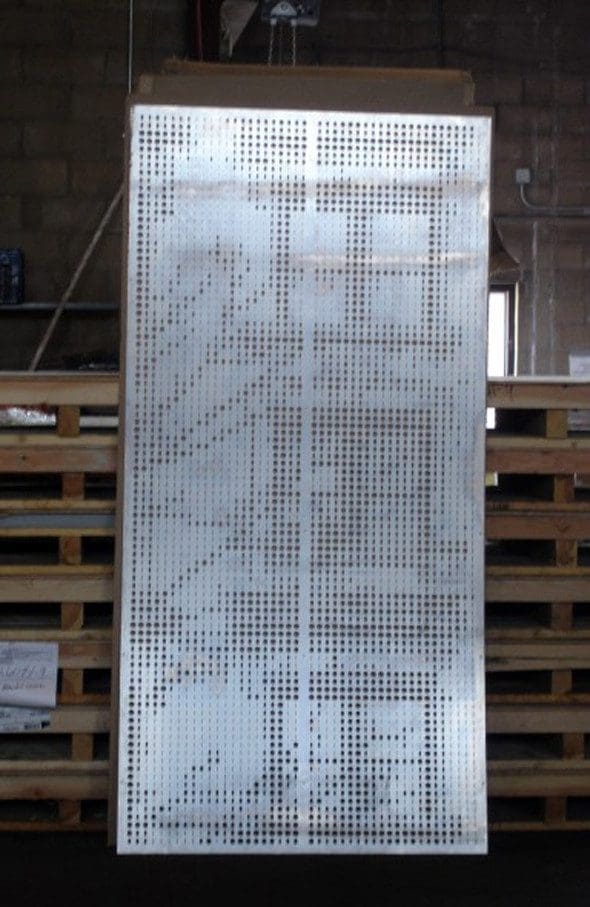
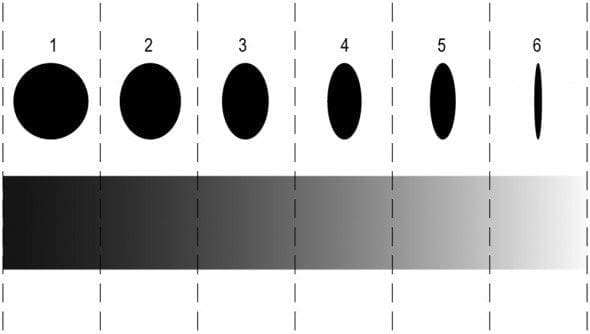
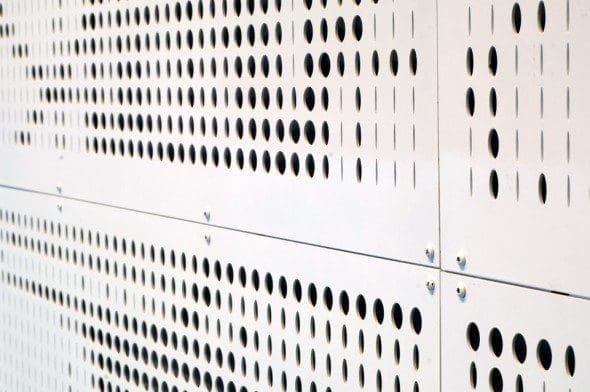
Surface 3:
Environmental Performance
Material: 16 ga. perforated, corrugated steel (powder-coated)
Performance Criteria: Optimization of sun shading, with the benchmark of eliminating 80% of solar head gain in the building.
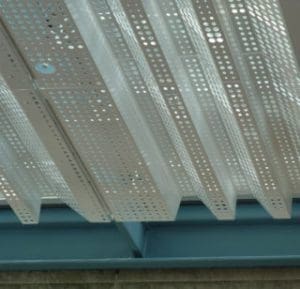
The ceiling for the new cafe addition, hung below a glass roof, is designed and engineered in conjunction with the low-E insulated glass to reduce the heat loads and allow for a more efficient conditioning system. Two strategies of patterning are used to develop the most efficient means of solar shading for the space: corrugation and perforation. Through a rigorous modeling and scripting process, the corrugation and perforation patterns were developed in tandem to optimize solar shading and reduction of solar heat gain inside the new building, while also achieving a more qualitative effect, evocative of a tree canopy.
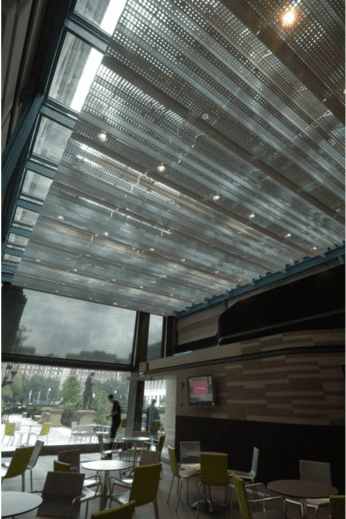
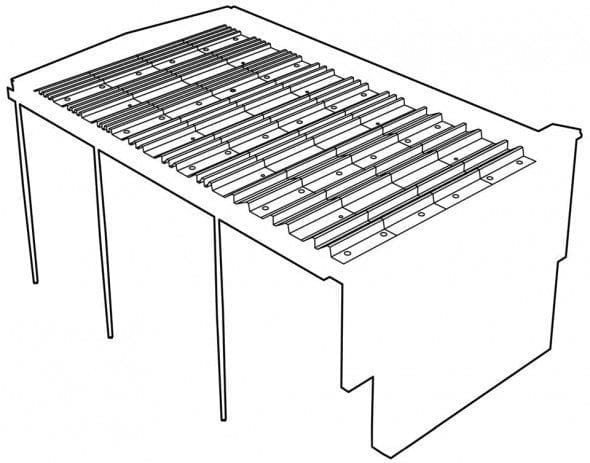
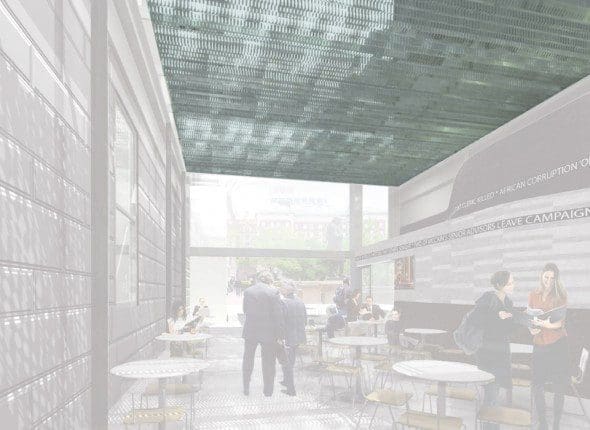
Pattern Generation: Corrugation Logic
A number of solar analyses were run on different days of the year to determine the environmental parameters of the site. The peak load—the point at which the direct solar radiation absorbed by the roof is the greatest—was identified through digital modeling, and this load became the benchmark by which the solar shading system was designed.
The sun angle information was in turn fed into an algorithm that generated the bend profiles of the ceiling panels. The basic principles of the script involved using the corrugations to block sunlight, while letting indirect light bounce and filter down to the space below. The script also adjusted the corrugations to provide space for lighting and sprinkler heads that are located above the ceiling panels.
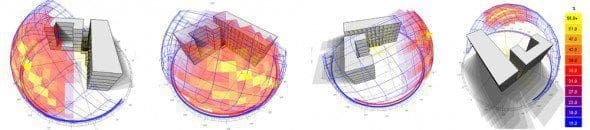

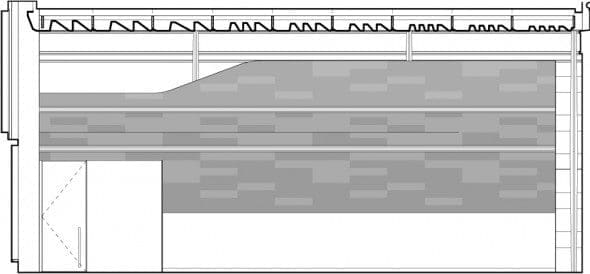
Pattern Generation: Perforation Logic & Cultural Overlay
Once the corrugation pattern was determined, the resultant geometry was fed back into the energy analysis software. Each segment of the panel (each face of the corrugated surface) was then assigned a maximum allowable percentage of perforation that would satisfy the 80% solar heat reduction requirement. The quantitative rules for the perforation pattern determined only the percent open, however, and not the actual pattern that drives how the holes are distributed to meet that benchmark percentage. The pattern itself was derived from an image of the sky (as if one was looking straight up from the cafe through the roof) and included an overlaid image of a satellite. The size and geometry of the perforations were determined by balancing the need for a resolution that would allow the image to be legible with the cost of laser cutting the holes in the panels.
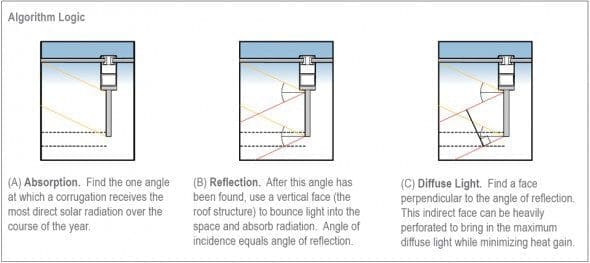

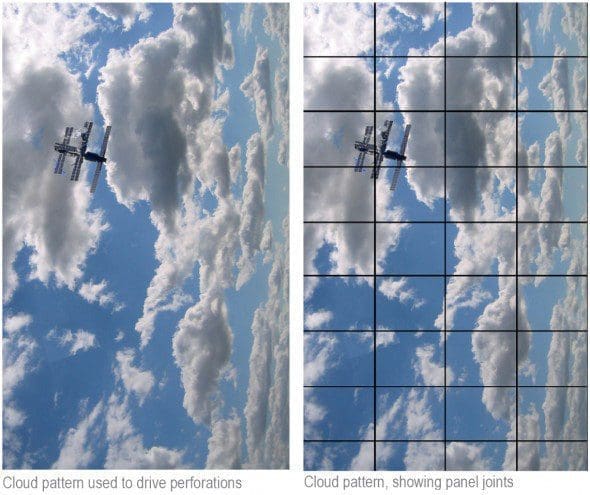


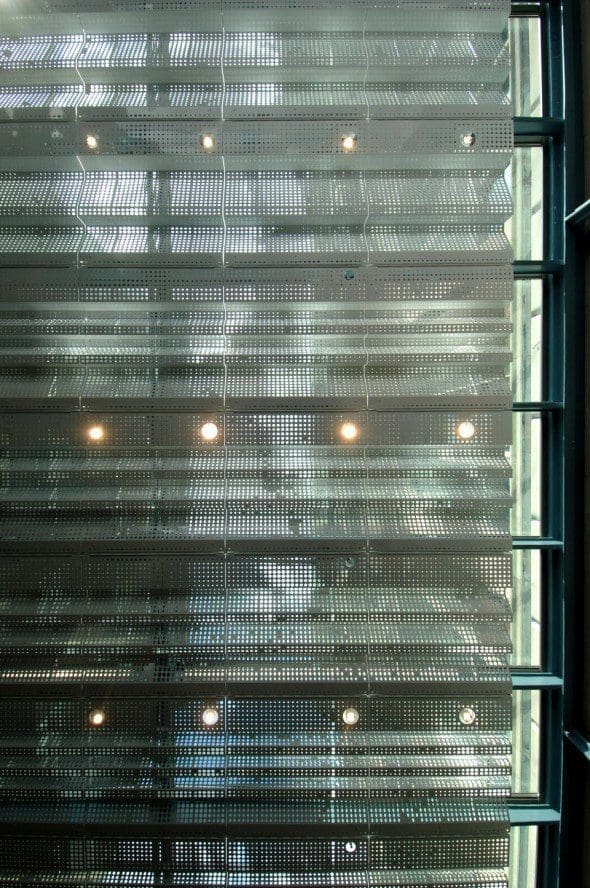
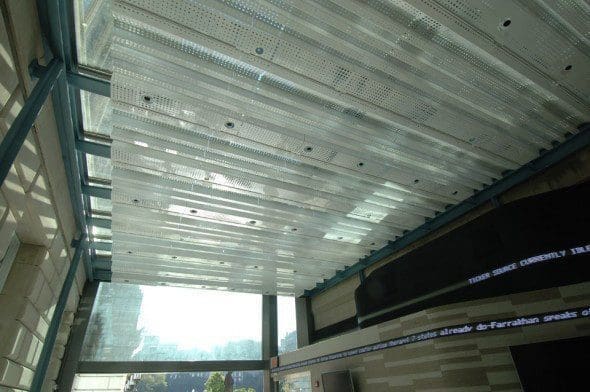
Surface 4: Dynamic Performance
Material: Steel frame; double laminated, insulated, heat-strengthened glass; stainless steel screw jack; computerized mechanism with safety devices
Performance Criteria: New facade on the University’s campus needs to maximize transparency, minimize structure, offer complete openness to the exterior in favorable weather, and satisfy all safety requirements.
The east facade of the new cafe addition, facing the University’s campus, was challenged with a set of performance criteria that was less quantifiable than with the other three surfaces in the project. In order to minimize impact on the McKim, Mead & White campus, the University asked that the design maximize its transparency and minimize its structure. An additional parameter of the design was programmatic: to allow the facade to literally open to the exterior in favorable weather, to extend the inside space of the cafe outside to the plaza.
The final design is comprised of three glass panels: two fixed transom pieces, and a lower glass wall (19′-0″W x 8′-6″H) that is motorized and rises up behind the transom, like a giant double-hung window. The main challenges to designing an operable glass wall involved the maximum possible sizes of procurable glass, the weight of the glass, the time needed to open the wall, and the safety precautions needed for lifting a 5-ton wall into the air. The resulting design produces its own kind of performance: the facade becomes an event in and of itself.
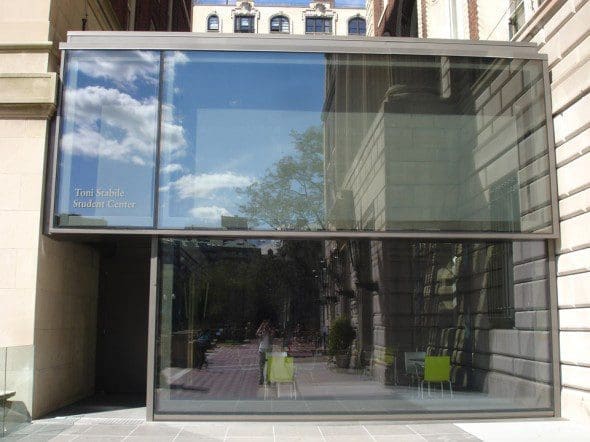
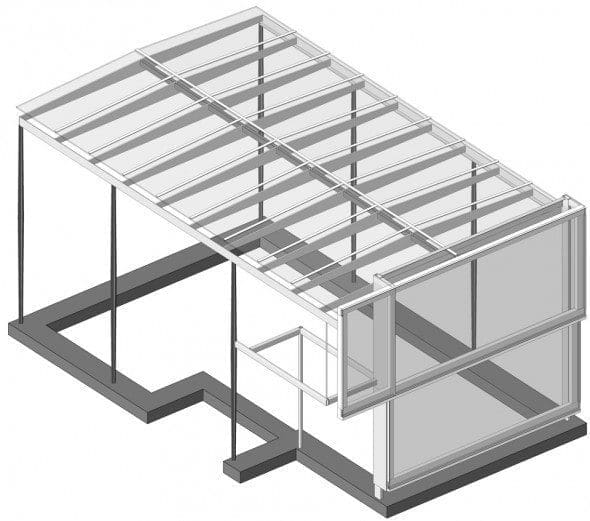
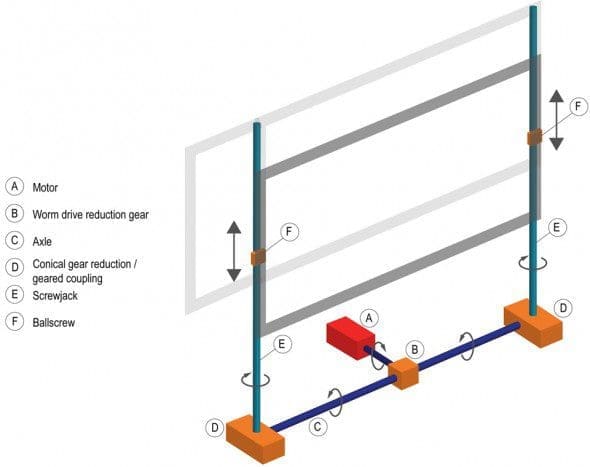
Testing Operation of Wall, Argentina; Detail of Screw Jack; Detail of Safety Sensor
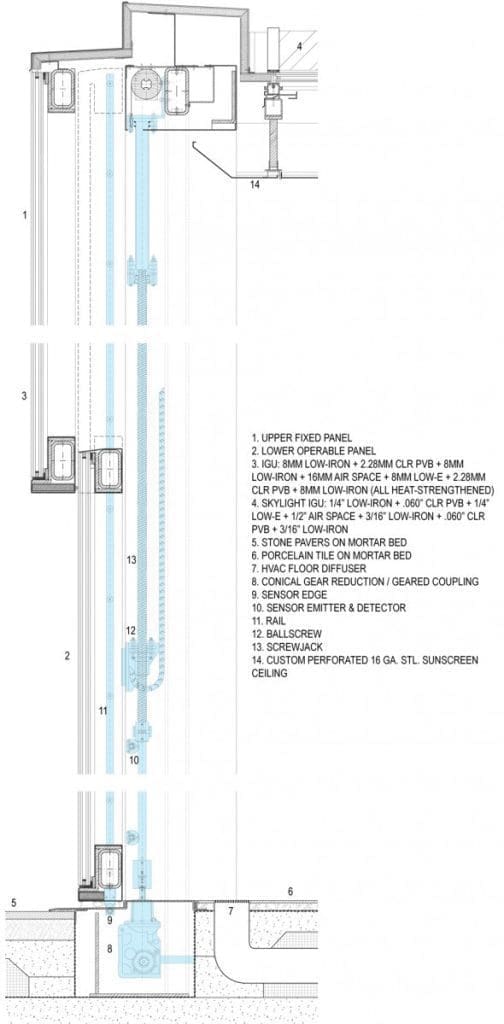
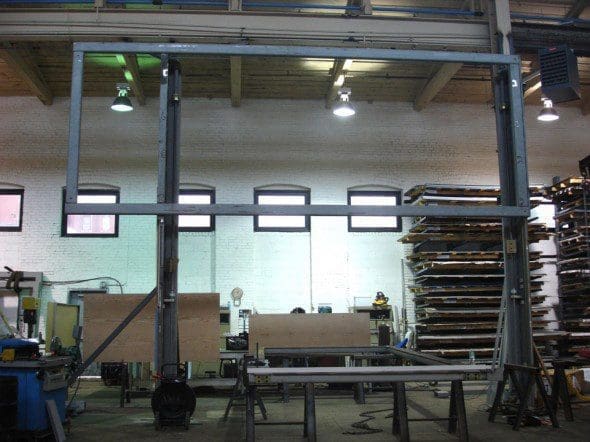
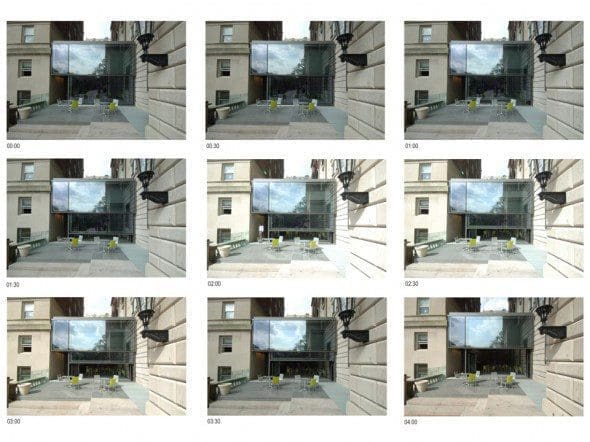
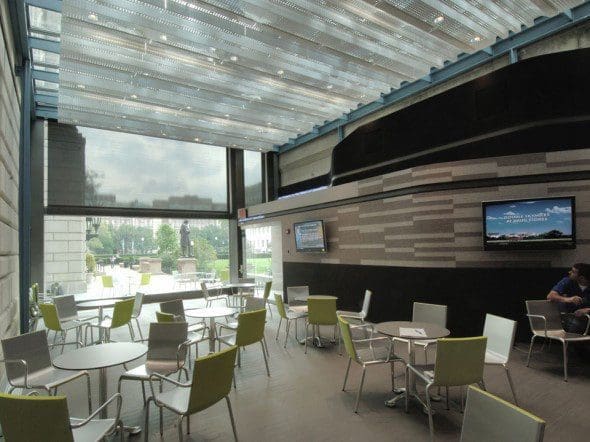
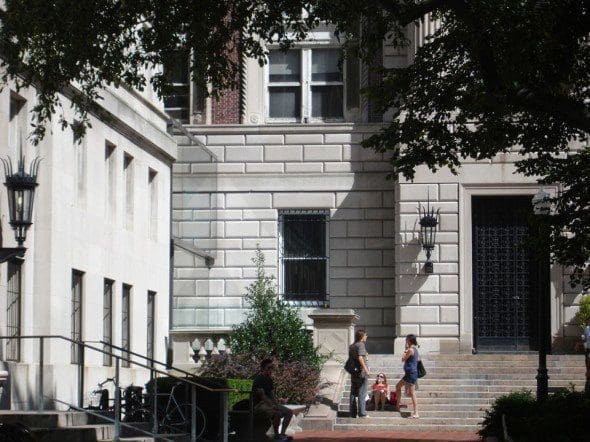
